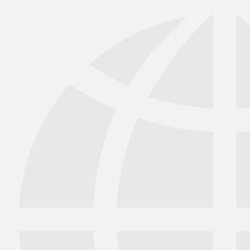
Van Bodegraven, Dutch supplier of electric motors, was able to use existing torque sensors and DAQ systems for designing a complete new test stand.
"Van Bodegraven Elektromotoren" in Dordrecht (the Netherlands) specializes in working with electric motors. The company supplies and installs new motors of various brands and has a workshop for carrying out repairs and overhauls. The test facility for electric motors at Van Bodegraven Elektromotoren has been using measuring equipment from HBK since 2016 to determine parameters including torque, rpm, voltage, and temperature.
“This enables us to make a sort of "ECG" for each motor,” states the manager, Richard Renee.
Van Bodegraven Elektromotoren, based in Dordrecht, is an established supplier of electric motors in the Netherlands, dealing in both new and refurbished motors. Around sixty percent of the company’s turnover comes from the maritime sector, and forty percent from the industrial sector. The motors are used for applications such as ship propulsion, as well as for driving pumps, fans, cranes, winches, anchor winches, and conveyor belts. This usually involves critical business applications, where a high level of reliability is required.
Van Bodegraven is an independent brand and supplies motors from manufacturers including ABB, Cantoni and Siemens. The company also has its own label Dormot, which comes from China. Chinese motors are somewhat more favorably priced and are mainly used for less critical applications. The make and type of motors that Van Bodegraven recommends to its clients depends largely on the application, of course.
According to Richard Renee, Van Bodegraven concentrates mainly on the replacement market.
“Large new build projects have become fairly rare in recent years unfortunately, and overhauls have also become a less frequent option. We have an extensive workshop where we repair, overhaul and modify motors, which makes up some 25 percent of our turnover. Overhauling an electric motor is no longer economically feasible in many cases. Motors rated up to about 45 kW have become much cheaper in recent years, so buying a new one is generally cheaper. Overhauls are only an option in the case of special motors that are no longer available or have a long lead-time. These include multi-speed motors, DC motors, or motors with special dimensions.”
“When we replace a motor, we do it on a one-for-one basis,” Renee continues “which means that a motor for a particular application is replaced by another. Supplying motors that exactly match the requirements for the specific application is crucial in the replacement market. They have to be delivered and installed quickly, for example, aboard ships that are loading and unloading their cargo in the Port of Rotterdam for the day. This means that we have to have the most common types of motors in stock, which cover hundreds of different brands. We also supply shafts and other components. We install motors on the clients’ premises and are increasingly employed to perform maintenance as well. Most of our mechanics are very enthusiastic about their profession, and know exactly how a motor is running when they feel it and hear it. We can also see that condition monitoring and predictive maintenance are becoming more and more important. We can read a motor’s status and performance remotely and wirelessly, which enables us to plan its maintenance. In the future, we will also be able to use measured data and our knowledge to predict when a problem can occur.”
Testing motors has grown in importance as a work process at Van Bodegraven. According to Renee,
“Many clients want to know in advance whether a motor meets the requirements in practice. This involves not just its performance, but also its energy efficiency, for example. We therefore brought a new, and one-hundred-percent vibration-free, test stand into use a year ago, whereby motors are tested under load in a vertical or horizontal position.”
Van Bodegraven uses torque sensors and measuring equipment from HBK in the test stand. Renee states,
“We looked closely at equipment from a number of suppliers and finally chose HBK. What is interesting is that we already bought an HBK T10F torque meter in 2004 and are still using it. It is rated at 5000 Nm. We have also bought a PMX measurement amplifier. This combination enables us to make simultaneous measurements of torque, rpm and temperature, as well as all electrical parameters such as voltage, current and power consumption. The measured data are read into the PMX modules in the analog form and are displayed on a screen using HBK’s catman Easy software, which makes the information easy for the client to understand as well. We provide them with a precise test report containing all the relevant graphs. In the new test rig, we also wanted to provide reliable measurements in the low torque range, and therefore purchased a new torque meter: the T40B with a nominal capacity of 500 Nm and with speed control. In addition to torque and speed, the meter also provides temperature, voltage and current readings and is also able to calculate energy consumption. The PMX data-acquisition and measurement system, together with the catman software from HBK, was the possible solution for our test setup. The modular nature of the measurement system, comprising of various measuring amplifier cards, renders the measurement and synchronization of all signals in the system a possibility.”
The measured values are read and digitized in the PMX measurement system. The system is then connected to a computer pre-installed with the catman software. The measured data is displayed real-time in chart forms, and visualized on the screen of the measuring chamber. This provides easily-comprehensible information for the customer, who may be observing the information over the operator’s shoulder. Besides displaying the information, the catman software also stores the measured values, allowing Van Bodegraven to calculate and assess the efficiency of the drive based on the asset data. The same data is utilized by the software to analyze trends, thereby providing the customer a comprehensive test report balence with all the relevant data.
Van Bodegraven’s test stand is also used a great deal by ABB, among others. ABB is a major supplier to Shell, which in turn has very demanding requirements for motors. The controllers for its motors use only Shell software; so, testing the combination of the controller and software is extremely important for motors destined for Shell plants. ABB test engineers run not only performance tests at Van Bodegraven, but also simulations and locked rotor tests. Heat run tests and endurance tests at full power can also be carried out. These tests are intended to show that the drivetrain (the motor plus the frequency controller) meets the client requirements.
Van Bodegraven has invested a great deal in this test stand. Heavy motors being tested at 100 percent load can cause severe vibration; therefore, a soil survey has been carried out to devising a way of coping with this. The result is that 12 piles have been driven as deep as 12 meters into the ground under the floor of the test stand to absorb the vibrations. This floor is not connected to the hall floor; so, the vibrations are not transmitted to the rest of the building.
In addition, Van Bodegraven can generate its own power of up to 600 kW on site (and even more with a number of adjustments), so that only losses from the mains are taken during tests. An additional test engineer, trained by HBK to work with the software and the test equipment, has been recruited for performing the tests. HBK also takes care of the annual calibration of the torque sensors and the PMX-system. The new test stand sets Van Bodegraven apart from its competitors in the region, all of whom lack a similar capacity for testing electric motors under load. The test stand is not yet in full-time use; so, Van Bodegraven will be happy to make it available to other suppliers.
A true family business. From the first generation to the current fourth, we believe that stagnation is decline. Energy is literally meant to move forward and further. And with the energy transition, at Van Bodegraven we aim to use more and more renewable sources. Your energy for tomorrow. We enjoy doing this for and with our customers, suppliers and employees.
Many clients want to know in advance whether a motor meets the requirements in practice. This involves not just its performance, but also its energy efficiency, for example. We therefore brought a new, and one-hundred-percent vibration-free, test stand into use a year ago, whereby motors are tested under load in a vertical or horizontal position. We looked closely at equipment from a number of suppliers and finally chose HBK.
This will bring together HBM, Brüel & Kjær, nCode, ReliaSoft, and Discom brands, helping you innovate faster for a cleaner, healthier, and more productive world.
This will bring together HBM, Brüel & Kjær, nCode, ReliaSoft, and Discom brands, helping you innovate faster for a cleaner, healthier, and more productive world.
This will bring together HBM, Brüel & Kjær, nCode, ReliaSoft, and Discom brands, helping you innovate faster for a cleaner, healthier, and more productive world.
This will bring together HBM, Brüel & Kjær, nCode, ReliaSoft, and Discom brands, helping you innovate faster for a cleaner, healthier, and more productive world.
This will bring together HBM, Brüel & Kjær, nCode, ReliaSoft, and Discom brands, helping you innovate faster for a cleaner, healthier, and more productive world.
This will bring together HBM, Brüel & Kjær, nCode, ReliaSoft, MicroStrain and Discom brands, helping you innovate faster for a cleaner, healthier, and more productive world.