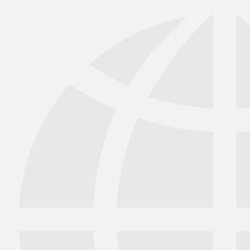
Schabmüller GmbH is the market leader in producing electric motors for mobile machinery. Together with HBK, Schabmüller has developed a new test-bench concept for a new type of drive. It combines the advantages of precise and cycle-accurate testing and measuring equipment with those of convenient test-bench development. This concept facilitates easily integrating sensors into the measurement system and controlling tests based on acquired data. Thanks to the formula database, which also provides formulas for real-time DSP calculation, the motor developer can quickly and easily create individual calculations – for customizable measuring and testing tasks.
Electric machines are the drives of today and the future. While the automotive industry still struggles with this transition, electric machines have been the standard in vehicles such as forklift trucks for over 50 years. Moreover, the requirements for motor performance and efficiency are continually rising. Hence, electric motor manufacturers work continuously to develop new drives. Simultaneously, new test-bench concepts are in demand to test these new motors with the required accuracy. The challenge is to obtain reliable results while precisely controlling test processes. Schabmüller GmbH, the world’s largest independent manufacturer of electric motors for battery-powered vehicles, also applies these requirements to its own test equipment. Together with HBK, the electric motor producer has developed a test-bench concept that enables measured data to be acquired and evaluated in line with these requirements. Schabmüller designs electric drives for forklift trucks, hybrid trucks and buses, as well as for construction and agricultural machinery. Schabmüller developers rely on HBK's extensive measurement technology in their new synchronous motor test bench, specifically the Genesis HighSpeed data acquisition system and the Perception software program.
A software program developed using National Instruments’ LabVIEW* development environment is deployed for automating and controlling the test bench. "The Genesis HighSpeed measurement system is exceptionally easy to work with and all processes run in parallel and in real time. This makes the development processes of our test bench software much easier and less complex," explains Dr. Martin Hafner, Manager of Technology Development for Permanent Magnet Synchronous Machines at Schabmüller. "Personnel expenses are considerably lower with Genesis HighSpeed in comparison to a measurement system based on National Instruments components alone."
As a driver of innovation in the industry, Schabmüller now also offers its customers permanent magnet synchronous electric motors. This new type of drive, without any changes to the cooling concept, produces just as much power as comparable asynchronous motors while requiring considerably less space. Optimizing or revising the cooling concept enables this effect to be disproportionately increased. To achieve this, synchronous motors must meet high requirements, be powerful and energy-efficient, and have a high energy conversion efficiency to optimally use the supplied energy. To ensure precise tests for the new electric drives, Schabmüller worked with HBK experts to optimize the test bench’s entire measurement chain.
"We chose the combination of Genesis HighSpeed and Perception software, as well as the LabVIEW development environment because Perception and LabVIEW are very easy to connect with an interface," according to Stefan Lauck, development engineer at Schabmüller. "Thanks to the Perception sensor database, we can also integrate a wide range of different sensors for current, voltage and torque into the measuring system quite easily, simply by plug-and-play, like inserting a USB device in a computer. Integrating vibration sensors as part of electrical measurement equipment is possible without any problems. That saves us time and resources in setting up the test bench."
The Schabmüller test bench is used for various measurement tasks to reliably determine the short-term or continuous power and energy conversion efficiency of synchronous machines, or to identify their service life and component reliability. Schabmüller experts measure rotational speed and torque, generate efficiency maps, and, based on this measured data, determine longitudinal and transverse inductances. Additionally, Schabmüller implements service life experiments under maximum mechanical stress. Long-term thermal experiments also determine how various long-term and interval loading patterns affect the motor function. "The electric motors have to achieve a service life of at least 50,000 hours," explains Stefan Lauck.
To securely and reliably determine all measured data, the test bench’s individual components must work together perfectly. The sensors acquire measurement signals such as current, voltage, temperature and torque and forward them to the data acquisition system. The Genesis HighSpeed GEN7tA data acquisition system is used on the Schabmüller test bench along with GN610B acquisition cards. The DSPs, digital signal processors on the cards, process the measured data and calculate the initial results in real-time. The calculated measurement results are forwarded to LabVIEW for analysis – at up to 1000 times per second thanks to the EtherCAT connection. In parallel, HBK’s Perception software also saves all the acquired raw data. "Measured data and real-time computing results are acquired and forwarded simultaneously and with the same time stamp. That's an enormous advantage for analysis," emphasizes Stefan Lauck.
Perception communicates with the LabVIEW software via a freely programmable software interface. The LabVIEW software is responsible for controlling and automating the test-bench processes. Based on real-time computing results, it controls the load and test specimen machines’ inverters. "The measured data can be processed for cycle-synchronous individual values. Then only the relevant cycle-synchronous computing results are used for control and automation of the test processes. For example, the RMS values of current and voltage or the torque values," says Stefan Lauck. "Since, if need be, the raw data will still be saved, we can also use it for more extensive post-process analyses." In addition to the cycle-synchronous individual values, continuously measured data can also be linked in the Perception formula database and processed in real time. No programming knowledge is required for this either.
"The combination of LabVIEW and HBK's Perception software really does offer us many advantages," says Stefan Lauck. "Genesis HighSpeed synchronously records measured data of sensors and allows for sample rates of up to 2 MS/s on up to 51 power channels. It automatically synchronizes the sample rates of the different channels and input cards. This considerably reduces users’ overhead. We were also able to make optimum use of LabVIEW advantages, such as the TDMS data format, to rapidly save large amounts of data. This also facilitates the subsequent data analysis using a wide range of available software products."
Schabmüller’s developers received customized support from HBK’s Perception experts as they integrated the data acquisition system into the test bench. According to Stefan Lauck: "Perception is an efficient software program that acquires data reliably. Thanks to the introductory training from HBK, we quickly became proficient. And because Perception is so easy to work with, we are able to define measurement sequences for our specific purposes."
Thanks to the Perception sensor database, a wide range of different sensors can be integrated into the measurement system simply by plug-and-play. Genesis HighSpeed reliably acquires measured data, calculates measurement results in real time, and makes them available for test-bench control. User-defined calculation formulas can be created without any programming knowledge and can also be applied to measured values in real time and to saved data in post process. This results in more efficient test processes with lower personnel expenses.
* LabVIEW is a trademark of National Instruments. Neither HBK, nor any software programs or other goods or services offered by HBK, are affiliated with, endorsed by, or sponsored by National Instruments.
Schabmüller GmbH is the world’s largest independent manufacturer of electric motors, producing more than 300,000 drives per year and having annual sales of over 90 million euros. The company from Berching, Bavaria, has been a supplier for international producers of forklift trucks, construction and agricultural machinery, as well as hybrid buses and trucks for over 50 years. For its range of forklift trucks, Schabmüller produces DC, asynchronous, and synchronous motors that are deployed as drives in propulsion and steering systems or pump motors for the mapping of lifting processes in these vehicles. One reason for the company's success – Schabmüller does not develop any standard motors, but instead, focuses on developing customer-specific and tailor-made motors for specific applications.
Perception is an efficient software program that acquires data reliably. Thanks to the introductory training from HBK, we quickly became proficient. And because Perception is so easy to work with, we are able to define measurement sequences for our specific purposes. We can also create our own formulas for the calculations in Perception and save them in the formula database. These formulas can be used in both post-process and real-time calculations in the DSPs, without any programming of the respective computer architecture.
The concept of separate power card and mainframe enables the remote probe closer proximity to the measurement object, thus reducing high-voltage cable length. This ensures any EMC is minimised while fibre optical cables enable fast, EMC-free and safe data transfer to the mainframe.
With a new family of fibre-optically isolated probes - available in 4 and 8 power channel packages and sample rates up to 20 MS/s - these probes are engineered for unrivalled accuracy.
This will bring together HBM, Brüel & Kjær, nCode, ReliaSoft, and Discom brands, helping you innovate faster for a cleaner, healthier, and more productive world.
This will bring together HBM, Brüel & Kjær, nCode, ReliaSoft, and Discom brands, helping you innovate faster for a cleaner, healthier, and more productive world.
This will bring together HBM, Brüel & Kjær, nCode, ReliaSoft, and Discom brands, helping you innovate faster for a cleaner, healthier, and more productive world.
This will bring together HBM, Brüel & Kjær, nCode, ReliaSoft, and Discom brands, helping you innovate faster for a cleaner, healthier, and more productive world.
This will bring together HBM, Brüel & Kjær, nCode, ReliaSoft, and Discom brands, helping you innovate faster for a cleaner, healthier, and more productive world.
This will bring together HBM, Brüel & Kjær, nCode, ReliaSoft, MicroStrain and Discom brands, helping you innovate faster for a cleaner, healthier, and more productive world.