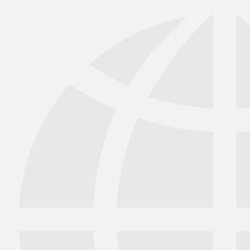
Learn which factors influence the accuracy of force measurements. This webinar will present an easy-to-use mathematical method to estimate the measurement uncertainty of a force measurement. We will also show some practical ways to improve the measurement uncertainty if required.
The following topics will be addressed:
Date: 2021 October 06th
Instructors: Thomas Kleckers (EU webinar) and Chris Novak (US webinar)
Duration: 40 minutes
Language: English
In general, every force transducer (that is, if we are talking about strain gauge-based sensors) works with every bridge amplifier. As well as the requirements for accuracy, the following points are also important:
TIP: An amplifier is usually an investment for more than a decade, so I would again recommend talking to the sales team.
We definitely recommend doing a rough uncertainty calculation before ordering the sensor to check which model fulfils the accuracy requirements. Contact the sales team if you are in doubt.
TIP: Load cells with high-end performance are not always expensive. HBK offers ‘S-type’ load cells (S2M and S9M) with outstanding accuracy at affordable prices.
Yes. Instruments have a linearity error, which is mostly very low. But there is a temperature dependence of the zero point and the amplification. The noise of the amplifiers also has an impact on the uncertainty of the measurement.
The resolution of the measurement chain is determined by the instrument. It only depends on the load cell in terms of the output signal it provides. If the signal is 100%, the whole resolution of the instrument is available. The limit of resolution of a load cell is given simply by the resistor noise of the load cell. In general, the higher the output of the load cell, the higher the resolution. The nearer the output signal of the load cell and the input range of the amplifier, the better the resolution.
TIP: HBK offers U15 and C15 load cells with a high output signal >4 mV/V and an amplifier system (QuantumX MX430B/MX238B) with matching input ranges. Ask your local sales engineer.
The result of our calculation is a range of force. In our first example we found out that if the measurement is 1000 N and the surroundings are as explained, the result is between 989 N and 1011 N. The probability that our real force is in this range is 68.27 %. That means that 31.77 % are outside this range.
In many cases this is not acceptable, and the target is to have a higher probability. So, we can double our force range from 1000 N ± 11 N to 1000 N ± 22 N. This means that more than 68.27 % of our measurements results are inside the new and larger interval. In our example 11 N is equal to k=1 and this is the first result. When doubling the range, this is k=2 and 95.45% of all measurements are in the new range. Tripling our 11 N will lead to a range from 967 N to 1033 N, and 99.73 % of all measurements show a reading inside this range. We call this k=3.
TIP: This principle is a consequence of the Gaussian function.
The calculation in the webinar was done based on the data sheet, which is a conservative approach, as the deviations (linearity, hysteresis…) are guaranteed to stay within the values specified there (at HBK, the sensors actually perform better than the values specified in the data sheet as these are the extremes). However, for a more precise calculation, a calibration certificate is preferable. It gives specific information about the linearity, repeatability, and hysteresis of the individual sensor, not the possible maximum. In other words, with a calibration certificate you know the real uncertainty of the sensor, which helps to improve the measurement uncertainty calculation.
If you have a calibration certificate, look for the uncertainty of the load cell at the load step that is interesting to you. You can add this error as an additional number to your calculation. As the linearity and the hysteresis are included in the uncertainty mentioned in the calibration certificate, you can leave them out.
TIP: Most calibration certificates mention the errors for k=2. Divide the uncertainty by 2 before putting it on your list. [Refer to the next question to find out more about k]
The competition might work differently, but at HBK, the accuracy class describes the biggest error for different characteristics such as linearity, hysteresis, TC0, creep… This makes sense as the biggest possible error is what determines the measurement uncertainty as well as the best possible results of the measurement.
You cannot use the accuracy class to calculate the measurement uncertainty, but the HBK accuracy class may help you with the sensible selection of the components of your measurement chain in terms of your budget and the given technical requirements.
Lateral forces usually have a negligible impact on the measurement, while bending moments are an important thing to consider in your calculation. Look at the data sheet for details. Estimate the value of the bending moment and calculate its individual error based on the formula shown in this webinar. Finally, the impact of the bending moment is just another number under the square root.
TIP: The influence of bending moments is related to full scale.
No. The GUM (Guide to the Expression of Uncertainty in Measurement) is the standard for measurement uncertainty calculation. The guideline can be used for all kinds of measurements (distance, weight, temperature…); it must, however, be adapted to the individual measurement problem.
TIP: We offer seminars on measurement uncertainty that will familiarize you with the uncertainty calculation of force or torque measurements and show you how to apply the guideline in a practical way.
This will bring together HBM, Brüel & Kjær, nCode, ReliaSoft, and Discom brands, helping you innovate faster for a cleaner, healthier, and more productive world.
This will bring together HBM, Brüel & Kjær, nCode, ReliaSoft, and Discom brands, helping you innovate faster for a cleaner, healthier, and more productive world.
This will bring together HBM, Brüel & Kjær, nCode, ReliaSoft, and Discom brands, helping you innovate faster for a cleaner, healthier, and more productive world.
This will bring together HBM, Brüel & Kjær, nCode, ReliaSoft, and Discom brands, helping you innovate faster for a cleaner, healthier, and more productive world.
This will bring together HBM, Brüel & Kjær, nCode, ReliaSoft, and Discom brands, helping you innovate faster for a cleaner, healthier, and more productive world.
This will bring together HBM, Brüel & Kjær, nCode, ReliaSoft, MicroStrain and Discom brands, helping you innovate faster for a cleaner, healthier, and more productive world.