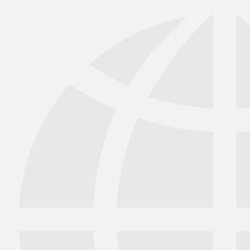
The independent test bench service provider APL has over 70 state-of-the-art motor and component test benches, and relies on HBK measurement technology.
APL tests motors, drive trains, drive train components and lubricants for customers in the automotive, oil and additives industries. This permits motors to be developed that consume less fuel with the same or even improved performance.
A realistic simulation of dynamic loads in vehicles is required for endurance testing or, alternatively, the identification of loss sources during efficiency tests on drive trains.
Motor design can be improved with the aid of such test data. However, reliable measurement technology is a prerequisite for obtaining meaningful test data.
During the development of the driveline test bench for rear-wheel drives, APL decided to use the HBK T40 torque transducer, impressed by its technology, economic efficiency, accuracy and small dimensions.
Torsional stiffness and mass moment of inertia influence the natural frequency of the overall system, comprising drive train and transducer, thereby affecting the measurable speed.
The compact design of the T40 torque transducer means that the drive train can be designed to be short and with high rigidity, which offers metrological advantages.
In addition, small and compact test benches save money as they require less floor space and smaller foundations.
The T40 has an accuracy class of 0.05 for temperature, repeatability and linearity, including hysteresis. In addition, the torque transducer also withstands the limit loads for longitudinal, transverse and bending moments.
The T40 has an output signal bandwidth of up to 6 kHz and an internal sampling rate of 38 kHz. This high sampling rate in comparison to the bandwidth, also called oversampling, helps to eliminate the effects of aliasing.
As the torque transducer is available with bandwidths of 1 kHz, 3 kHz and 6 kHz, high investment security is also achieved. It can be integrated into existing systems, due to the compatibility with 1 kHz-conditioning electronics, as well as in demanding dynamic applications.
Last but not least, the good price/performance ratio makes the T40 highly suitable for use in dynamic
applications such as the test benches at APL.
Automation and robotics often require signal conditioning in real time and a direct data exchange with superordinate controllers via fieldbus.
The T40 is the first transducer with a Torque Measurement Communication interface (TMC), which can be upgraded with digital interfaces using the TIM40 torque interface module which enables communication with the automation system via CAN, EtherCAT or Profibus.
With cutting-edge technology and highly efficient processes, our employees have been working successfully as engineering service providers for over 30 years for a worldwide clientele from the automotive, oil, fuel and additives industries.
This will bring together HBM, Brüel & Kjær, nCode, ReliaSoft, and Discom brands, helping you innovate faster for a cleaner, healthier, and more productive world.
This will bring together HBM, Brüel & Kjær, nCode, ReliaSoft, and Discom brands, helping you innovate faster for a cleaner, healthier, and more productive world.
This will bring together HBM, Brüel & Kjær, nCode, ReliaSoft, and Discom brands, helping you innovate faster for a cleaner, healthier, and more productive world.
This will bring together HBM, Brüel & Kjær, nCode, ReliaSoft, and Discom brands, helping you innovate faster for a cleaner, healthier, and more productive world.
This will bring together HBM, Brüel & Kjær, nCode, ReliaSoft, and Discom brands, helping you innovate faster for a cleaner, healthier, and more productive world.
This will bring together HBM, Brüel & Kjær, nCode, ReliaSoft, MicroStrain and Discom brands, helping you innovate faster for a cleaner, healthier, and more productive world.