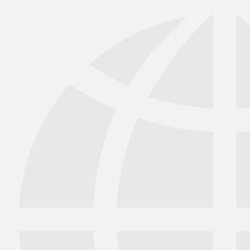
Tunnels are at the core of our infrastructure. They are found in large cities, mountains and even underwater. They provide connections and shorten distances. But how safe are they?
Today, modern monitoring systems allow reliable condition monitoring of tunnels using fiber Bragg technology.
Mechanical deformations in a tunnel can present a significant safety hazard particularly during construction work on the tunnel itself or in its immediate surroundings. It is essential to quickly check the stability and reliability of the structure.
When choosing the sensor technology to be used for tunnel monitoring it is necessary to consider the following challenges:
For all the above, optical sensor technology, based on fiber Bragg technology, has developed into a powerful alternative to conventional monitoring systems.
Fiber Bragg sensors measure physical quantities, such as strain, with light. In addition to its outstanding long-term stability, the technology offers another major advantage: it enables measured values to be transmitted over long distances, with virtually no loss in measurement quality. Furthermore, a single optical waveguide can accommodate several fiber Bragg sensors, thus reducing the effort needed to set up the monitoring system to a minimum. This is a crucial aspect, particularly when monitoring tunnels that often are many kilometres long. Moreover, the system can be used for gathering measurements during regular operation of the tunnel without interfering with traffic.
HBK offers tunnel monitoring solutions that enable users to take full advantage of the benefits of using fiber Bragg sensors for tunnel monitoring.
For a complete tunnel monitoring system the following components should be considered:
Sensors for measuring strain and temperature, installed on the tunnel lining. Sensors can be welded to the metallic girders, embedded into concrete walls or glued to the surface. These 'sensor rings' can be installed in different tunnel sections and are connected to one another with fiber optical cables.
Interrogators for processing the light signals
Software for processing the measured data
Fiber optic measurement systems are suited to both long-term monitoring and shorter measurement cycles. The system can be used during regular operation – as illustrated by the examples of the Rossio tunnel and the São Paulo Metro tunnel, where the MEMCOT method (see application note for further information) was used for estimating convergences between measurement points.
HBK measurement systems are a reliable solution for continuous use. This means that they not "only" acquire measurement data reliably and long term, but also enable automatic alarms to be configured for significant changes to the tunnel geometry. Systems can be built with off-the-shelf products or adjusted according to your specific needs with the support of our custom systems team. Contact us!
More information can be found in our Application Note: Optical Monitoring System for Strain and Convergence Measurement (PDF).
Isso reunirá as marcas HBM, Brüel & Kjær, nCode, ReliaSoft e Discom, ajudando o senhor a inovar mais rapidamente para um mundo mais limpo, mais saudável e mais produtivo.
Isso reunirá as marcas HBM, Brüel & Kjær, nCode, ReliaSoft e Discom, ajudando o senhor a inovar mais rapidamente para um mundo mais limpo, mais saudável e mais produtivo.
Isso reunirá as marcas HBM, Brüel & Kjær, nCode, ReliaSoft e Discom, ajudando o senhor a inovar mais rapidamente para um mundo mais limpo, mais saudável e mais produtivo.
Isso reunirá as marcas HBM, Brüel & Kjær, nCode, ReliaSoft e Discom, ajudando o senhor a inovar mais rapidamente para um mundo mais limpo, mais saudável e mais produtivo.
Isso reunirá as marcas HBM, Brüel & Kjær, nCode, ReliaSoft e Discom, ajudando o senhor a inovar mais rapidamente para um mundo mais limpo, mais saudável e mais produtivo.