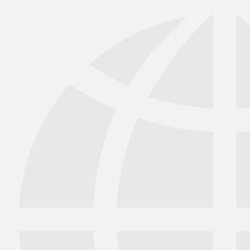
Effective production line testing ensures customer acceptance and maintains product brand value, production line yield and cost effectiveness by ensuring that finished products comply with the expectations set during R&D, that product quality is consistent and that root causes for faults are mitigated.
Manufacturers care about the product quality they can achieve in their production. Whether they build one satellite a year, thousands of aircraft engines, or millions of microchips, finished products must perform to R&D specifications and customer expectations. If not, they risk low yield, product safety issues, costly recalls, warranty claims, and damage to their brand.
Effective quality assurance (QA) requires you to relate the product to the performance achieved by designers in R&D. Some deviations from the ideal may not affect the product, and may be deemed to be within bounds, but others might affect the entire machine or system, or even endanger end-user health and safety.
The type of testing chosen depends on the production volume, complexity of the product, the amount of time needed to test, and the consequences of a failure.
Depending on the potential consequences, testing may be automated, standardized and fast, or represent a more complicated in-depth analysis. Each scenario presents a set of choices that must be made to achieve the best cost-benefit and quality level.
Brüel & Kjær offers proven systems, designed for your industry and that can be customized for your requirements to best fit your production line and goals. Please get in touch with our engineering experts, for any questions regarding assessing the optimal testing setup for your requirements.
Isso reunirá as marcas HBM, Brüel & Kjær, nCode, ReliaSoft e Discom, ajudando o senhor a inovar mais rapidamente para um mundo mais limpo, mais saudável e mais produtivo.
Isso reunirá as marcas HBM, Brüel & Kjær, nCode, ReliaSoft e Discom, ajudando o senhor a inovar mais rapidamente para um mundo mais limpo, mais saudável e mais produtivo.
Isso reunirá as marcas HBM, Brüel & Kjær, nCode, ReliaSoft e Discom, ajudando o senhor a inovar mais rapidamente para um mundo mais limpo, mais saudável e mais produtivo.
Isso reunirá as marcas HBM, Brüel & Kjær, nCode, ReliaSoft e Discom, ajudando o senhor a inovar mais rapidamente para um mundo mais limpo, mais saudável e mais produtivo.
Isso reunirá as marcas HBM, Brüel & Kjær, nCode, ReliaSoft e Discom, ajudando o senhor a inovar mais rapidamente para um mundo mais limpo, mais saudável e mais produtivo.